the feedstock.
This is where it all starts, the feedstock: a mix of polymers and fine metal powder. At Demcon MIM, we develop our own unique, biodegradable feedstock, allowing us to use different metal alloys. The feedstock is a thermoplastic, metal-filled material that can be processed using standard injection moulding techniques. We were one of the first MIM manufacturers to use a water-degradable feedstock system. While our competitors rely on toxic solvents or acids to process their feedstock, we simply use an infinitely available, harmless liquid: water. This difference for the feedstock, which in our case is also biodegradable, gives us a huge advantage when it comes to reducing the environmental impact of the metal injection moulding process.
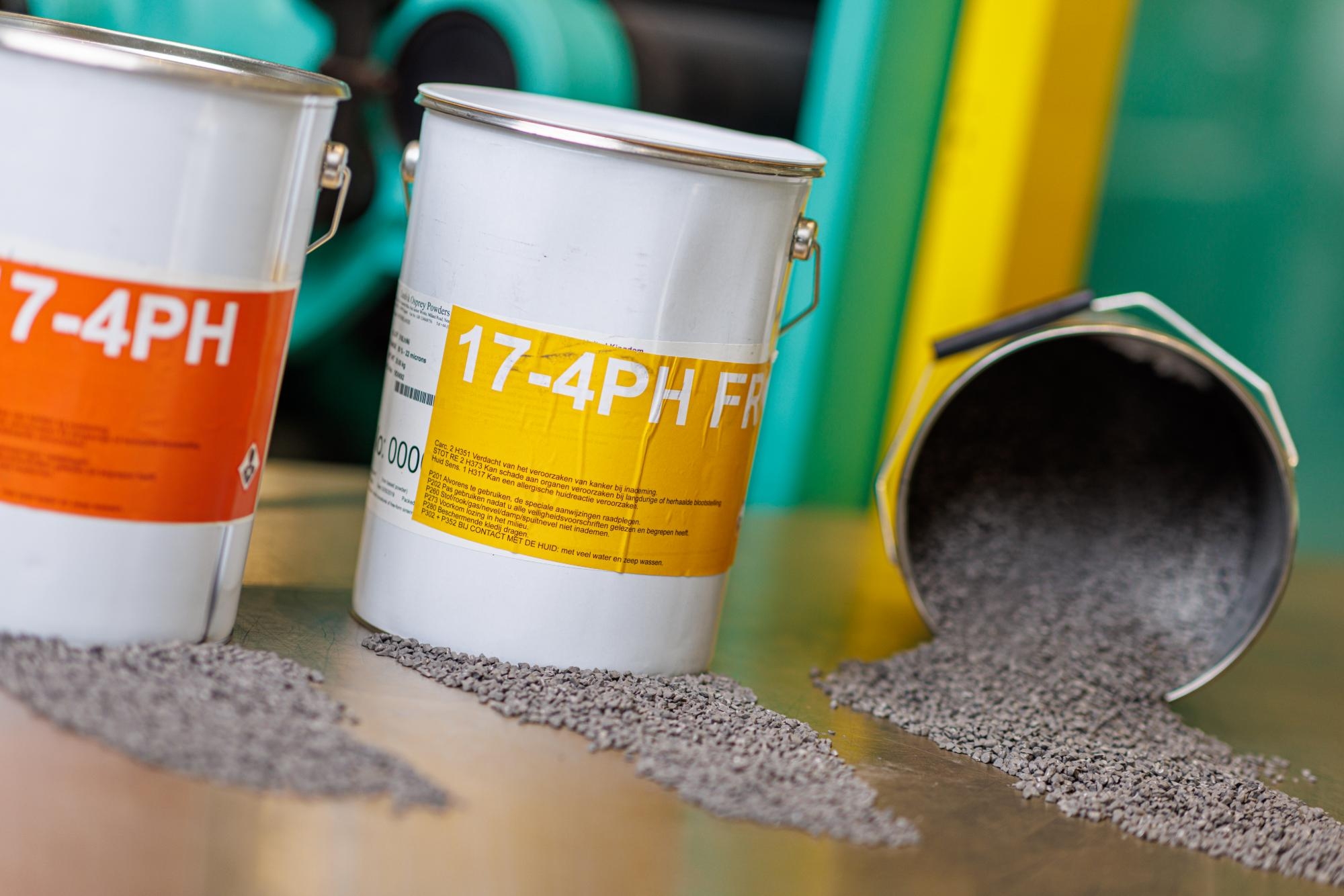
sintering.
The brown parts are porous and fragile parts. To achieve the final strength, surface smoothness and dimensions, they are heated to high temperatures in special ovens. This process called sintering binds the metal powder together, creating a dense metal part and giving it its strength. During the sintering process, the part shrinks about 13%. With our feedstock, the shrinkage rate is significantly lower than with commercial feedstocks, where 18% shrinkage occurs. The advantage of this is less deformation and better tolerances. We already include the 13% shrinkage in the mold design.
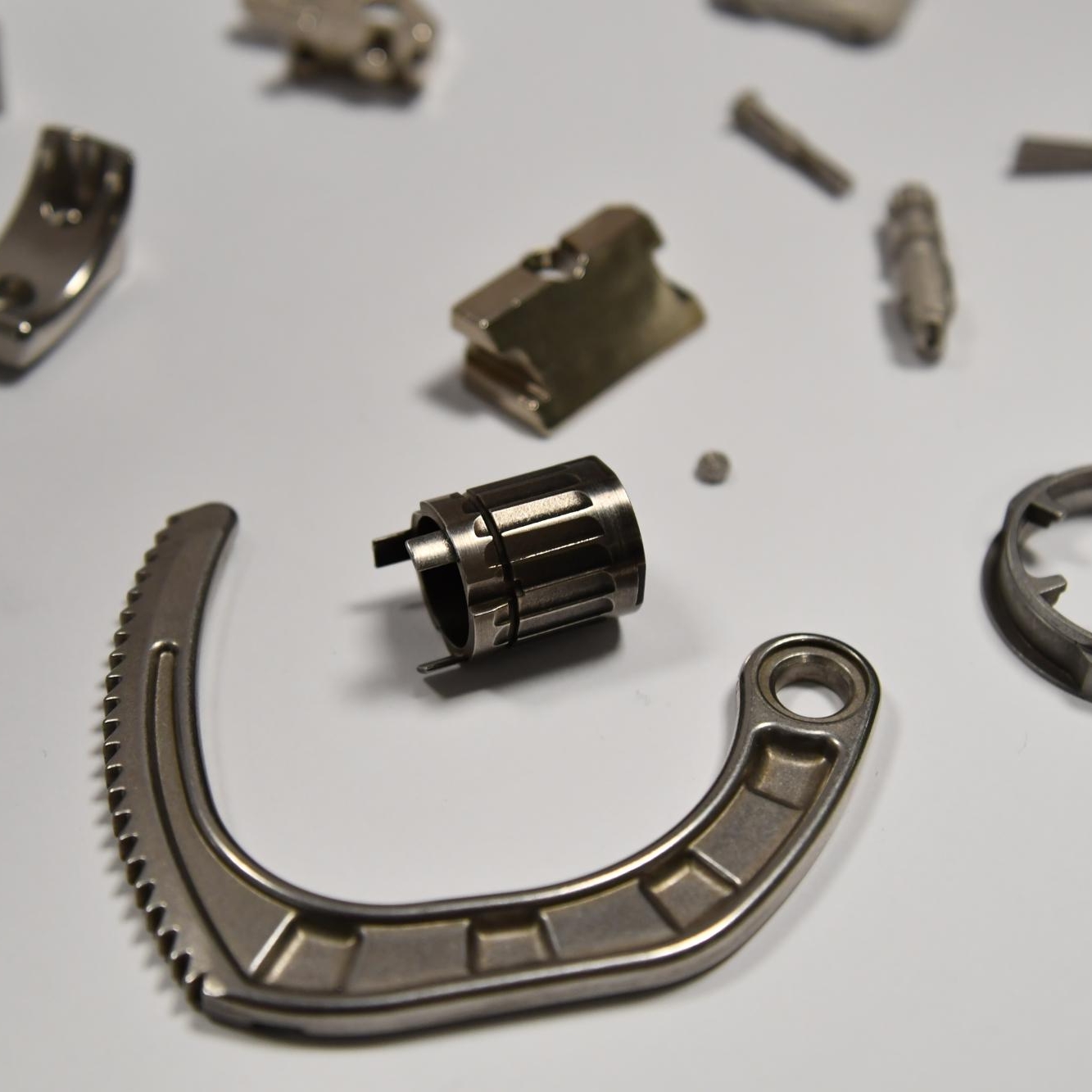
why choose Demcon metal injection moulding?
reduced ecological footprint.
At Demcon MIM, we put a lot of energy into reducing our carbon footprint. For our own feedstock, we can use a biodegradable polymer and environmentally friendly debinding techniques. This allows us to use water rather than harmful chemicals to dissolve the polymer. Also, no toxic gases are released when heating the products to debind the remaining polymer. Furthermore, because MIM is a “net-shape” manufacturing technique, little waste material is generated. With all production taking place in the Netherlands and due to a strong local network of suppliers, transportation remains limited. Thanks to this broad commitment, Demcon MIM has achieved ISO 14001 certification and we can help customers further reduce their carbon footprint.
more than just a manufacturing company.
At Demcon MIM, we strive to provide broad support to our customers. This means that we not only manufacture parts, but also produce feasibility studies for parts and materials and ensure optimal design. Check out our services and discover how we can help solve problems. In doing so, we can join forces with the Demcon group and our strategic partners. This makes Demcon MIM a company that can offer customers advanced solutions for complex parts.
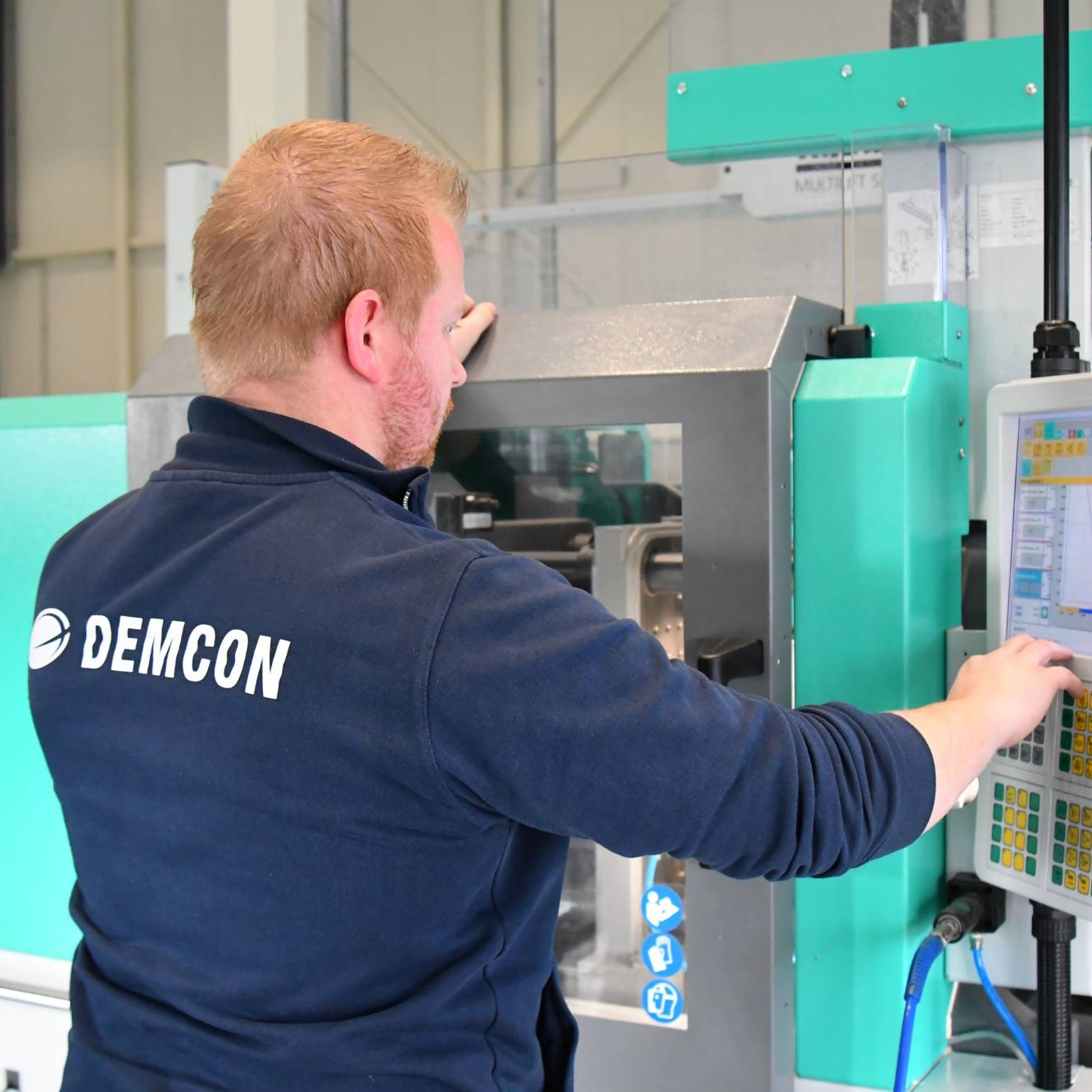