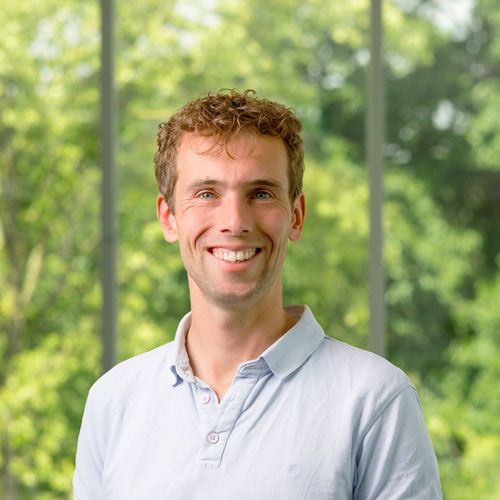
highlights
- marking of injection-moulded parts
- safe and reliable
- invisible and non-removable
- various applications for identification
growing market.
Adding an optical fingerprint to products is taking off in many markets, from luxury goods to industrial components or textile products. The aim may be to prevent counterfeiting, facilitate quality control or enable identification for recycling. Products that lend themselves to optical fingerprinting include luxury watches, buckles of expensive bags, links of high-end bracelets and decorative logos for exclusive handbags. But identification can also be useful for critical industrial parts that are often replicated, such as bearings and gears.
homogeneous distribution.
To make the most of the advantages of optical fingerprinting, we started a collaboration with Tailorlux. We have developed a new production process for invisibly marked metal products. For this, we add Tailorlux’ inorganic marking pigment to our MIM raw material. This allows us to produce invisibly marked metal products in an efficient process, without the need for an additional post-production step for marking. Moreover, the pigment is homogeneously distributed in the cast metal product, so the marking cannot be removed and is not lost through wear and tear.
“higher added value from MIM.”
Thanks to the high sensitivity of the Tailorlux scanners and the strong fluorescence signal of the pigment, only a small amount of marking material is needed for a measurable response. We can therefore reliably cast, deburr and sinter the resulting raw material according to standard procedures in our certified process. The favourable product properties, such as high tensile strength, hardness and corrosion resistance, are maintained during the process.
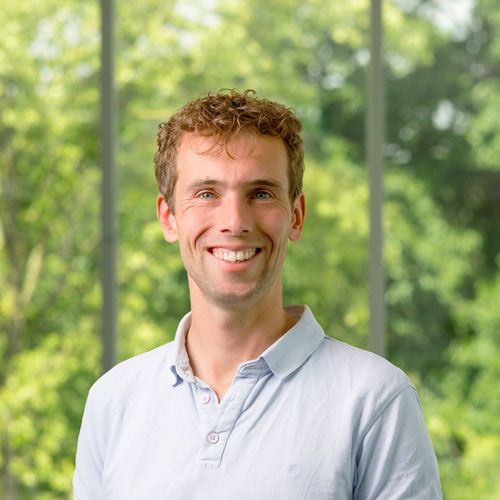