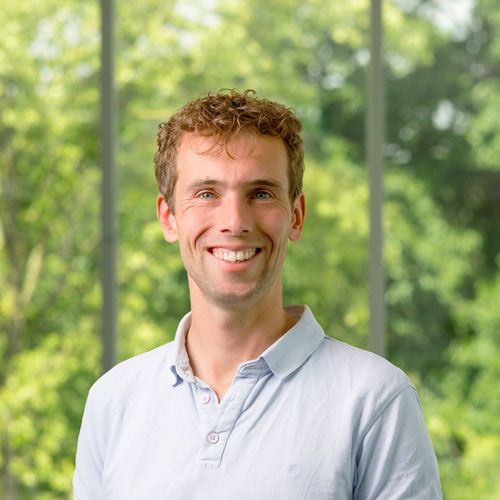
highlights
- safe and reliable
- light and strong
- lower environmental impact
- extra functionality
lower weight, smaller footprint.
While the traditional design relied on cast aluminum and machined stainless-steel parts, the new handcuffs are produced from die-cast magnesium parts and stainless steel MIM parts. This combination reduces the weight by 30% compared to the old design, whilst improving the strength of the handcuffs. In addition, the production of the new handcuff has a lower environmental impact: the footprint of the MIM parts is up to 22% smaller than their machined counterparts.
added functionality.
Each handcuff contains ten parts produced with our metal injection moulding technology. MIM’s freedom of form allows us to add additional functionality to the design, such as larger keys (also made with MIM) for motorcycle officers wearing gloves. Another example is a dry Teflon coating on moving parts. This has the advantage that dust is easily removed, much better than parts coated with oil or grease.
“our handcuffs are reliable and safe.”
Handcuffs must be usable in all possible conditions, whilst being exposed to high tensile forces of up to 4,500 N. Our colleagues at Demcon multiphysics have simulated how handcuffs react to stress or deformation. By cleverly adding or removing material, we achieved greater strength and flexibility whilst meeting safety requirements. After the successful completion of the design process, the production of all MIM parts, including assembly of the final product, was transferred to Demcon metal injection moulding.
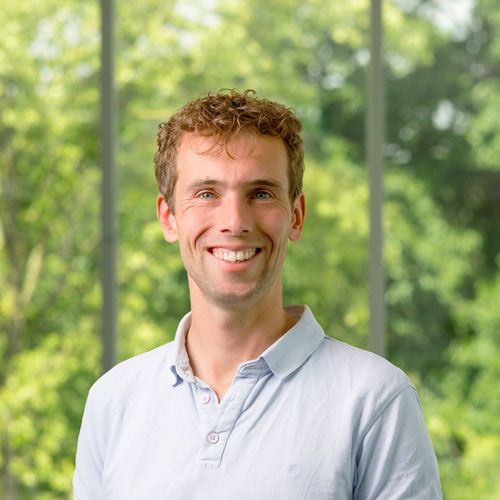