de feedstock.
Dit is waar het allemaal mee start, de feedstock: een mix van polymeren en fijn metaalpoeder. Bij Demcon MIM ontwikkelen we onze eigen unieke, biodegradeerbare feedstock. Daarmee zijn we vrij in het gebruik van verschillende metaallegeringen. De feedstock is een thermoplastisch, metaalgevuld materiaal dat kan worden verwerkt met standaardspuitgiettechnieken. Wij waren een van de eerste MIM-fabrikanten die een waterafbreekbaar feedstocksysteem gebruikten. Terwijl onze concurrenten afhankelijk zijn van giftige oplosmiddelen of zuren om hun feedstock te kunnen verwerken, gebruiken wij simpelweg een onbeperkt beschikbare, onschadelijke vloeistof: water. Dit verschil voor de feedstock, die bij ons ook nog eens biodegradeerbaar is, geeft ons een groot voordeel als het gaat om het verminderen van de milieubelasting van het metaalspuitgietproces.
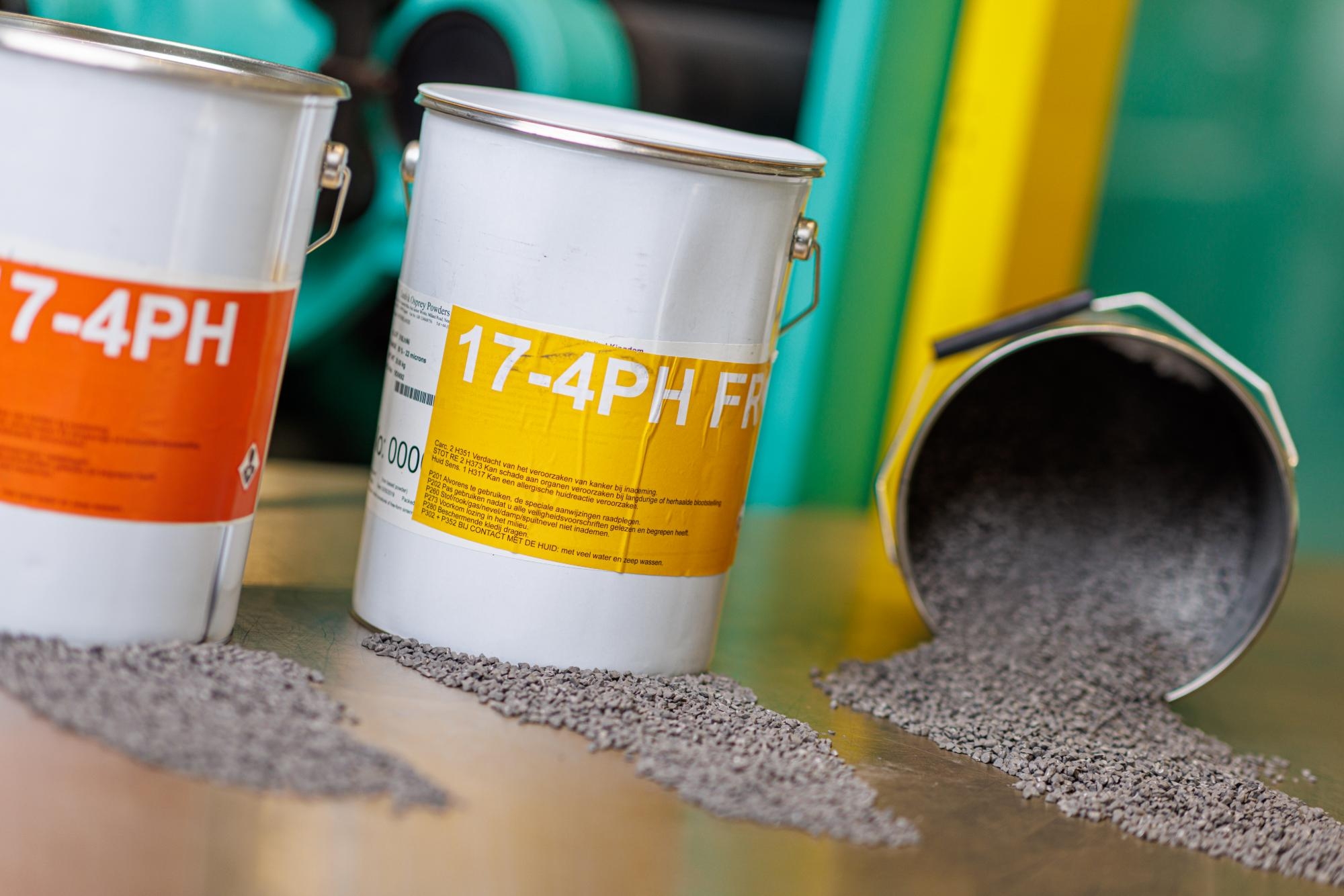
sinteren.
Bruinlingen zijn poreuze en fragiele onderdelen. Om de uiteindelijke sterkte, oppervlaktegladheid en dimensies te bereiken, worden ze in speciale ovens verhit tot hoge temperaturen. Door dit proces, sinteren, bindt het metaalpoeder aan elkaar; dat zorgt voor een dicht metalen onderdeel en geeft het zijn sterkte. Tijdens het sinterproces krimpt het onderdeel ongeveer 13%. Met onze feedstock ligt het krimppercentage duidelijk lager dan bij commerciële feedstocks, waarmee 18% krimp optreedt. Het voordeel hiervan is dat er minder vervorming optreedt en de toleranties beter zijn. Wij nemen de 13% krimp al mee in het ontwerp van de matrijs.
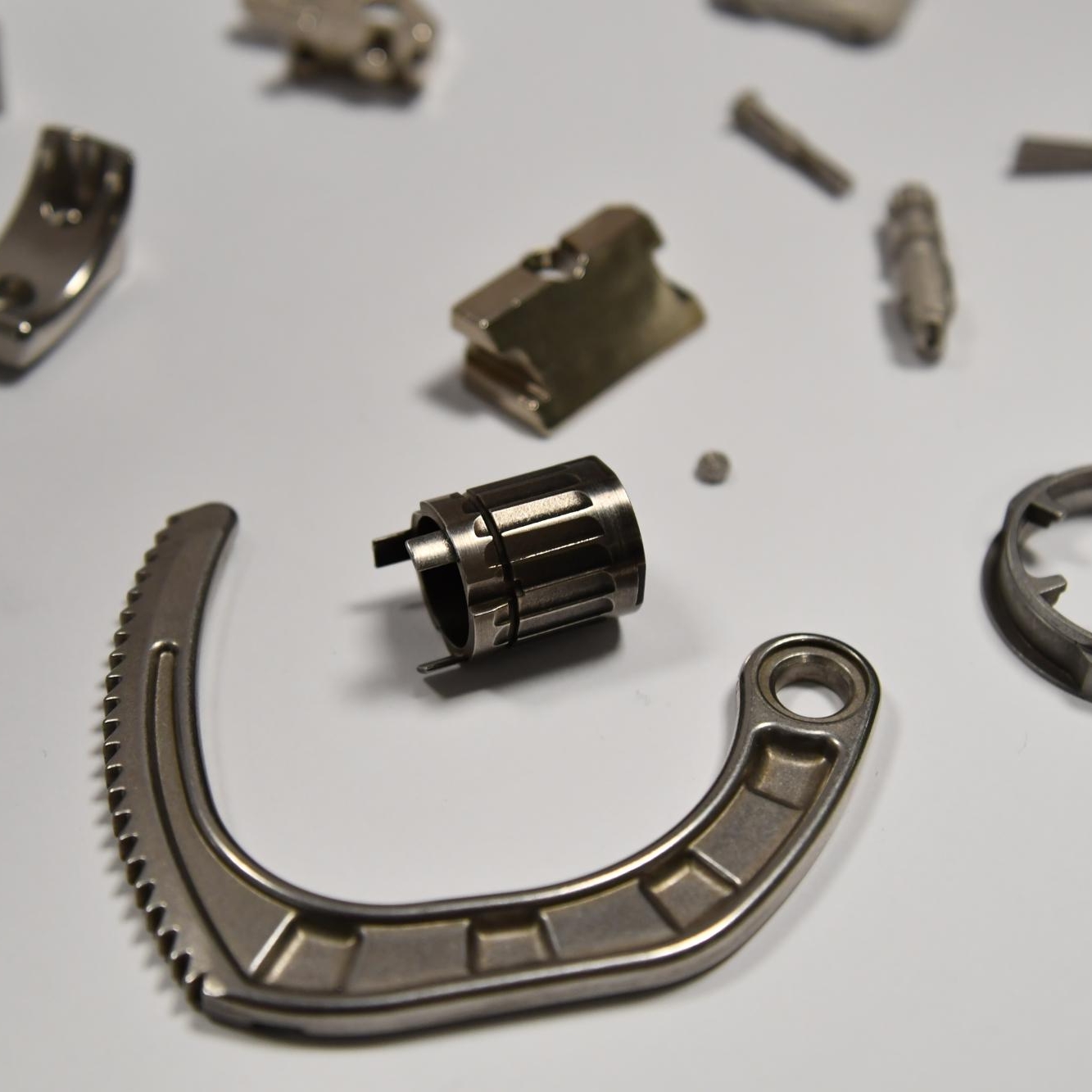
waarom kiezen voor Demcon metal injection moulding?
beperkte ecologisch voetafdruk.
Bij Demcon MIM hebben we veel energie gestoken in het verkleinen van onze ecologische voetafdruk. Voor onze eigen feedstock kunnen we een biologisch afbreekbaar polymeer en milieuvriendelijke debindtechnieken gebruiken. Hierdoor kunnen we water gebruiken om het polymeer op te lossen, in plaats van met schadelijke chemicaliën te werken. Ook komen er geen giftige gassen vrij bij het verwarmen van de producten om het resterende polymeer te debinden. Bovendien, omdat MIM een ‘net-shape’ productietechniek is, ontstaat er weinig afvalmateriaal. Doordat alle productie in Nederland plaatsvindt en we een sterk lokaal netwerk van leveranciers hebben, blijft het transport beperkt. Dankzij deze brede inzet heeft Demcon MIM de ISO 14001 certificering behaald en kunnen wij klanten helpen hun ecologische voetafdruk verder te verkleinen.
meer dan alleen een productiebedrijf.
Bij Demcon MIM streven we ernaar om onze klanten breed te ondersteunen. Dit betekent dat wij niet alleen onderdelen vervaardigen, maar ook haalbaarheidsstudies voor onderdelen en materialen verzorgen en voor een optimaal ontwerp zorgen. Bekijk onze diensten en ontdek hoe wij kunnen helpen bij het oplossen van problemen. Daarbij kunnen we de krachten bundelen met de Demcon group en onze strategische partners. Dit maakt Demcon MIM tot een bedrijf dat klanten geavanceerde oplossingen kan bieden voor complexe onderdelen.
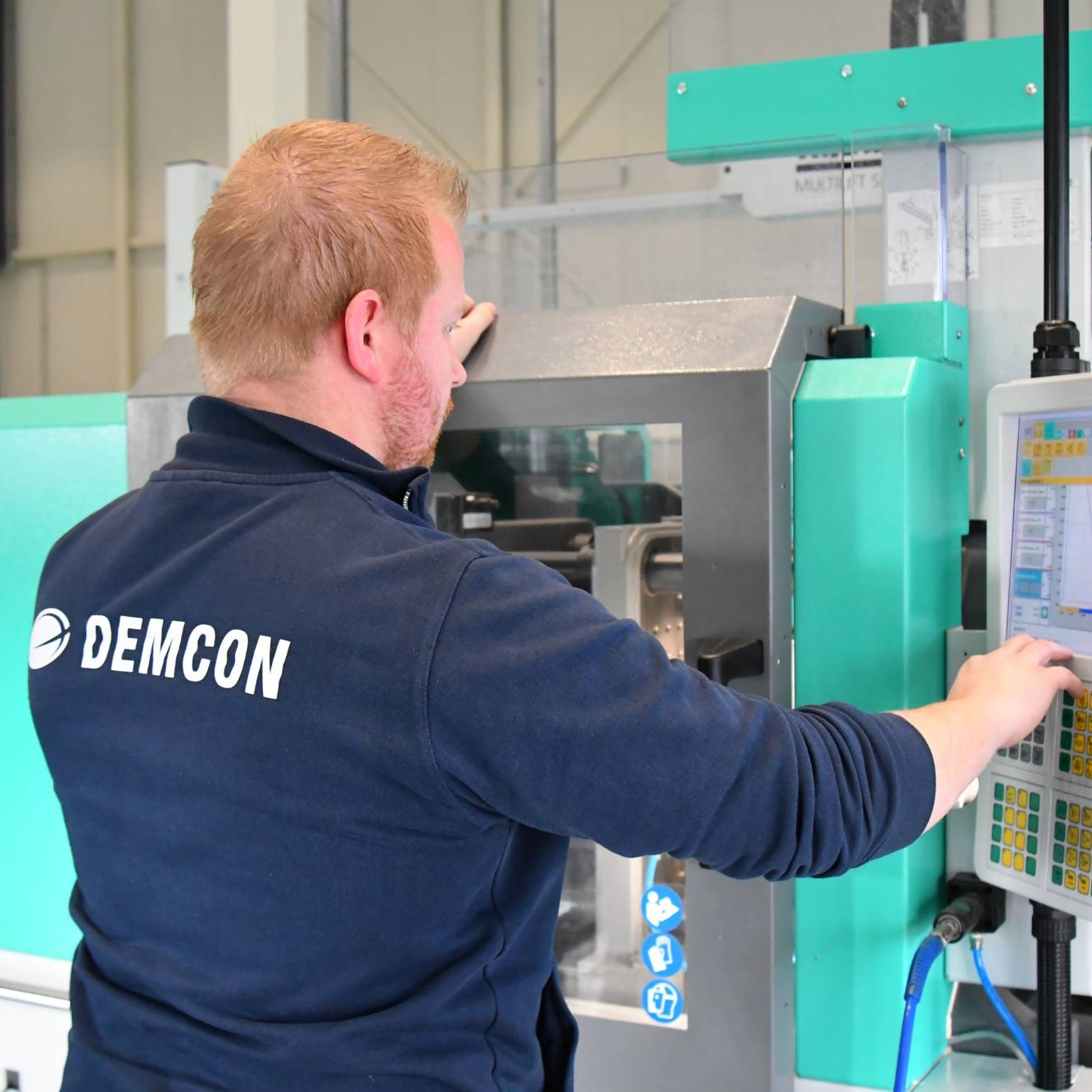